Laser Focus on TIG Welding
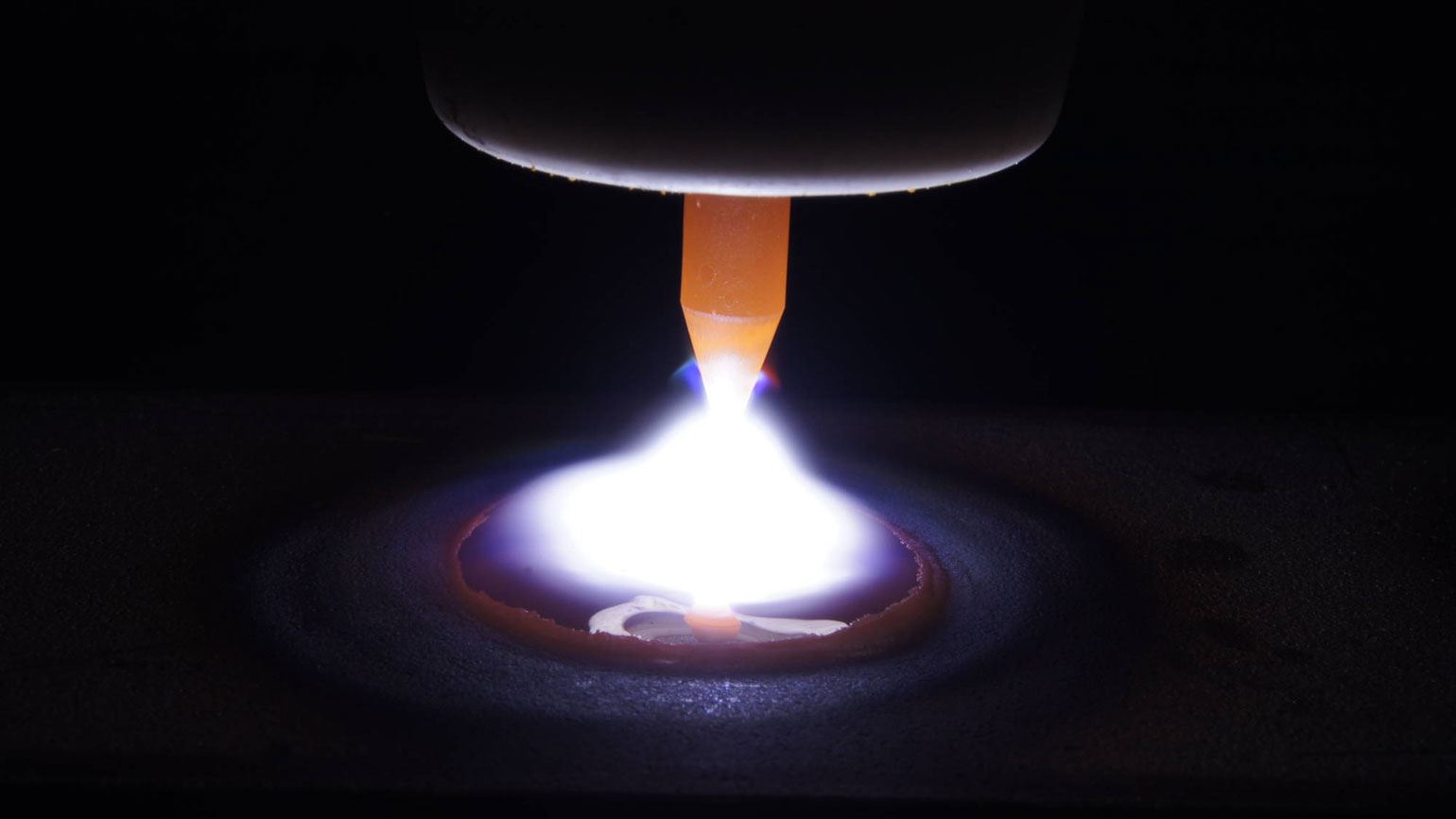
History:
Welding is the most commonly used method in joining metal parts since ancient times, blacksmithing was one of the famous arts used for making small boxes made of Iron that were welding by hammering. Sir Murphy Davy in 1800 produced an arc between two carbon electrodes using battery, and in late 1800 gas welding and cutting was developed which became a practical joining process. In 1880’s Auguste De Meritens from Cabot Laboratory in France used the heat of an arc for joining lead plates for storage batteries but his pupil Nikolai N. Benardos from French Laboratory was granted a patent for welding, this was beginning of carbon arc welding. In 1890, C.L. Coffin of Detroit was awarded the first U.S. patent for using metal electrode for an arc welding method. This was the first record of the metal melted from the electrode carried across the arc to deposit filler metal in the joint to make a weld. In 1900 Strohmenger and others introduced a coated metal electrode, World War 1 brought huge demand and it was an opportunity to setup welding companies. Automatic welding was introduced in 1920’s by using bare electrode wire on Direct Current and used arc voltage for regulating feed rate. In 1930’s Stung Welding was developed, an idea by C L Coffin to weld in non-oxidizing gas atmosphere was refined by H M Hobart who used helium for shielding, the process was ideal for welding magnesium, stainless steel and Aluminum, in 1941 it was perfected by Meredith and named as Heliarc Welding. In 1950’s CO2 welding was familiar. Pulsed Current and use of small amounts of oxygen was introduced in 1960’s. Most recently Friction welding using rotational speed and upset pressure to provide friction heating was developed. Laser technologies were one of the newest methods used for cutting metals, nonmetals and also welding. [1]
In 1940’s the TIG welding was very popular and gained name very rapidly because they could weld magnesium and Aluminum, we shall understand and the technique of TIG welding the most famous method. Beltecno uses TIG welding method to manufacture the SS Tanks which helps our water to be hygienic always.
Tungsten Inert Gas Welding:
Process: Arc welding and TIG welding works on same principle, High intense arc is generated between tungsten electrode and workpiece, arc generates heat energy used to join metal by fusion, to prevent surface from oxidation a shielding gas is used.
TIG Welding Process [2]
Power source with high current drawing capacities are used as power source, the unit can be driven by both AC and DC depending the material we need to TIG, For Stainless Steel, Mild Steel, Titanium, Copper etc., DC Current is utilized, for Magnesium and Aluminum we need to use AC current. The operating voltages wary from 10V to 30V and approximately 250-350 A of current to generate the arc. [3]
The welding is done using a troch with the electrode and nozzle, usually the electrode tip is sharp which allows the high intensity current to pass and efficiently weld the joint. Enormous amount of heat is exchanged during the process, henceforth we need to efficiently employ a method to cool the torch, usually we use water or air. As name suggests Inert gas is usually used to protect the weld zone from oxidization, which means the inert gas will not allow weld joint to be exposed to oxygen. Electrodes are called as filler material, depending upon the application we can choose the grade and type of the filler material.
Advantages:
- Dissimilar metals can easily be welded
- Provides very good weld strength and finish
- Heat input can be varied to weld both thin and thick sample sections but usually thick samples can’t be welded
- The system can be made to operate on both automatic and manual mode
- Skilled fabricator can easily reduce the heat affected zones and also produce a very good and fine surface finish
- Low complexity on maintenance and operations.
Beltecno uses TIG welding method to manufacture the stainless steel tanks which are very efficient towards cost and operations.
References:
[1] https://www.millerwelds.com/resources/article-library/the-history-of-welding
Get your tank price