Beltecno Storage Tanks: The Ultimate Choice for the Beverage Industry
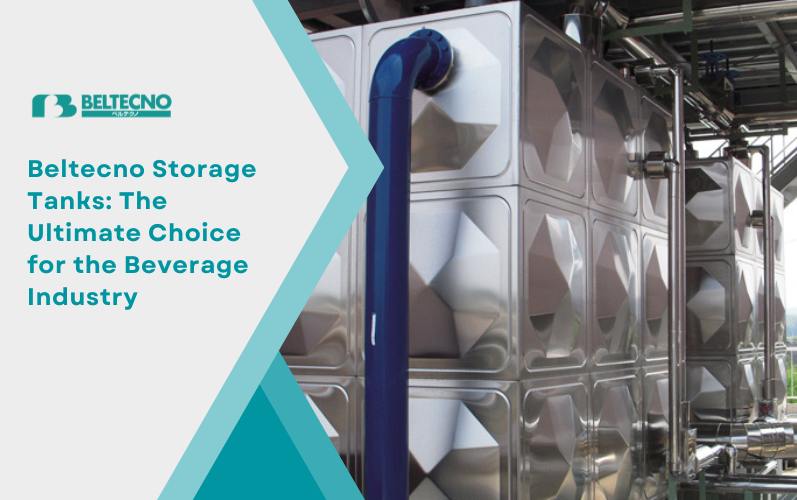
When it comes to beverages, quality is everything.
Behind the scenes, however, ensuring this consistency is no small feat. One of the biggest, and often underestimated, challenges the beverage industry faces is safe water storage and temperature control during storage.
Temperature fluctuations in storage tanks can lead to spoilage, loss of flavor, and reduced shelf life, problems that frustrate consumers and cost the beverage industry millions annually.
For decision-makers in the beverage industry, the stakes are high. Inefficient storage systems directly impact product quality, customer trust, and operational costs.
Storing Clean and Processed Water for Beverage Production
Maintaining water purity is critical for beverage production. Contaminated water can impact the final product's taste, safety, and overall quality.
Storage tanks made from materials like plastic or concrete are particularly prone to issues like microbial growth and chemical leaching. Over time, this can lead to severe problems that affect both production and compliance with regulatory standards.
Traditional storage tanks like RC water tanks are often porous, creating an ideal environment for bacteria, algae, and mold to thrive. In warm climates or during prolonged storage, these microorganisms multiply rapidly, compromising water quality.
Additionally, non-food-grade materials can leach harmful chemicals into the water, which affects flavor as well as poses health risks. Frequent cleaning of such tanks is necessary to mitigate these risks, but it increases operational downtime and labor costs.
Stainless steel storage tanks address these challenges with their non-porous, corrosion-resistant surface. Unlike plastic or concrete, stainless steel does not absorb or harbor contaminants.
This means water stored in stainless steel tanks remains clean and free from unwanted microbial growth or chemical leaching. Beltecno's stainless steel tanks are certified food-grade, ensuring the highest level of hygiene for beverage production.
Temperature stability is another critical factor in water storage. Poorly insulated tanks allow heat transfer, leading to fluctuating water temperatures that increase energy consumption and disrupt production processes.
Let’s explore how temperature control can transform the way beverages are stored—and why stainless steel tanks are the key to success.
The Role of Temperature Control in Beverage Storage
Effective temperature control in storage tanks is essential for preserving the chemical, microbial, and physical integrity of beverages. Without it, products can deteriorate quickly, leading to spoilage and customer dissatisfaction. Below, we analyze five key areas where temperature regulation directly impacts beverage storage.
1. Preserving Flavor and Aroma
Temperature fluctuations wreak havoc on the delicate chemical compounds that define a beverage’s flavor and aroma.
Temperature control protects the sensory experience customers expect, ensuring flavors remain authentic and fresh.
2. Preventing Microbial Growth
Microbial contamination is one of the biggest threats to beverage safety and shelf life. Temperature regulation is a natural and effective way to mitigate this risk.
Regulatory standards demand that beverages be stored within strict temperature ranges to maintain safety. A deviation of even a few degrees can render a product unsellable.
3. Maintaining Physical and Visual Stability
The appearance and texture of a beverage are just as important as its taste. Temperature shifts can cause visual and physical changes that make a product unappealing to consumers.
Temperature Effects on Beverage Stability |
||
Beverage Type |
High Temp Effect |
Low Temp Effect |
Wine |
Oxidation, flat flavors |
Suppressed aroma |
Beer |
Stale taste, skunky aroma |
Sedimentation |
Dairy Drinks |
Spoilage, bacterial growth |
Protein and fat separation |
Carbonated Drinks |
Loss of carbonation |
Reduced fizz |
4. Extending Shelf Life
Temperature control directly impacts shelf life by slowing down the natural breakdown of beverage components.
5. Reducing Financial Losses
Beyond quality, temperature mismanagement can lead to significant financial losses through product recalls, wastage, and reduced customer loyalty. Spoilage and recalls due to poor storage conditions are expensive.
For large-scale beverage producers, these losses quickly add up. Temperature control reduces waste and improves profitability while ensuring consistent quality.
How Stainless Steel Storage Tanks Optimize Temperature Control
Stainless steel tanks remain the benchmark for excellence in temperature-controlled beverage storage. Beltecno Global’s advanced design and material properties address the unique challenges of maintaining consistent temperatures while processing beverages. It enhances hygiene, durability, and scalability.
1. Excellent Thermal Conductivity
As shown in the image, applying glass wool insulation to tanks minimizes thermal radiation and ensures consistent temperature retention.
With only a 2.3°C temperature drop over 8 hours in extreme conditions (0°C outdoor temperature and 80°C tank interior), this insulation significantly reduces heat transfer.
This capability ensures that stored beverages maintain consistent temperatures, highlighting the importance of using effective insulating materials like glass wool for temperature stability.
2. Hygienic and Non-Reactive Surface
Stainless steel is non-porous, inhibiting bacterial growth and minimizing chemical reactions. This is especially important in the production process of acidic beverages. It also provides easy cleaning as the smooth surface prevents residue buildup, making cleaning quick and efficient.
"Stainless steel tanks are a long-term investment in beverage quality and safety.” – Beltecno Global
3. Modular and Scalable Design
Beltecno’s storage tanks offer modularity, allowing businesses to scale storage capacity as production grows.
4. Durability and Long-Term Cost Savings
While stainless steel tanks may have higher upfront costs, their durability, and low maintenance requirements result in significant long-term savings.
-
Lifespan: Stainless steel storage tanks last decades, reducing the need for frequent replacements.
-
Minimal Repairs: Their corrosion resistance eliminates costly repairs caused by rust or leaks.
Energy Efficiency and Sustainability in Temperature Control
Consumers and regulatory agencies increasingly demand eco-friendly practices, and companies must respond by minimizing energy use and environmental impact without compromising product quality.
Let’s re-imagine beverage industry temperature control through energy-efficient, sustainable practices.
1. Insulated Stainless Steel Tanks Reduce Energy Loss
One of the most effective ways to save energy in temperature control is through high-performance insulation.
-
Minimizing Heat Exchange: Stainless steel tanks with advanced insulation significantly reduce the transfer of heat between the stored beverage and the external environment. This keeps internal temperatures stable with minimal energy input.
2. Reducing Waste Through Shelf-Life Extension
Precise temperature control not only saves energy but also reduces beverage waste. By preventing spoilage and extending shelf life, companies can optimize production and distribution.
-
Food Waste Reduction: Up to 20% of beverage spoilage worldwide occurs due to improper storage production processes. Reducing spoilage supports global sustainability goals while boosting profitability.
3. 100% Recyclable Materials for a Circular Economy
Stainless steel is an inherently sustainable material. Tanks made from stainless steel are:
-
Long-Lasting: Their durability ensures decades of use, reducing the need for frequent replacements.
-
Fully Recyclable: At the end of their lifecycle, stainless steel tanks can be recycled, contributing to a circular manufacturing economy.
Energy efficiency and sustainability go hand in hand, and stainless steel tanks provide a practical, long-term solution for businesses aiming to meet environmental and operational goals. One such solution is highlighted in the Benefits of Insulated Water Tanks for Industries, which underscores how these tanks contribute to both energy conservation and sustainable practices.
The Challenges of Temperature Control and How to Overcome Them
High initial investments and retrofitting challenges in older facilities can hinder efficient temperature control in beverage storage. This analysis explores common obstacles and offers actionable solutions for decision-makers.
1. High Initial Investment in Modern Temperature Control Systems
One of the primary barriers for many beverage manufacturers is the upfront cost of upgrading to temperature control systems. Stainless steel tanks with integrated cooling or insulation require a higher initial expenditure compared to traditional materials like plastic or aluminum.
Why This Is a Challenge
-
Smaller businesses or startups may struggle to allocate funds for these upgrades.
-
The perception that short-term cost savings outweigh long-term benefits discourages investment.
-
Facilities often lack the financial flexibility to replace outdated systems all at once.
How to Overcome It
-
Modular Solutions: Beltecno’s stainless steel panel tanks offer a modular design that allows businesses to scale storage capacity gradually. Companies can start small and expand over time without sacrificing quality or efficiency.
-
Long-Term ROI: While the upfront cost is higher, stainless steel storage tanks significantly reduce energy consumption, maintenance expenses, and product spoilage, making them a more economical choice in the long run.
2. Retrofitting Existing Facilities with Modern Systems
Older facilities often lack the infrastructure to support advanced cooling or heating systems, making retrofitting a challenging task.
Why This Is a Challenge
-
Limited space for new tanks or equipment.
-
Incompatibility between existing systems and modern solutions.
-
Potential downtime during retrofitting processes disrupts production schedules.
How to Overcome It
-
Customizable Designs: Beltecno’s stainless steel panel tanks are designed for easy installation in facilities with space or infrastructure limitations. Their modular assembly ensures they fit seamlessly into existing setups.
3. Maintenance and Operational Complexity
Temperature control systems often require regular maintenance to operate efficiently, which can place a strain on resources, particularly for facilities with high production volumes.
Why This Is a Challenge
-
Regular cleaning and upkeep are labor-intensive, especially for porous materials like plastic that are prone to microbial buildup.
-
Downtime during maintenance affects production timelines.
-
Complex systems require trained personnel for operation and troubleshooting.
How to Overcome It
-
Low-Maintenance Materials: Stainless steel’s non-porous surface resists corrosion and microbial growth, reducing cleaning frequency and effort.
4. Seasonal Production and Demand Fluctuations
Many beverage manufacturers face seasonal spikes in demand, such as during summer months or holiday seasons. These fluctuations can strain storage systems and cooling capacities during the production process.
Why This Is a Challenge
-
Insufficient storage capacity during peak production periods leads to inefficiencies and higher spoilage rates.
-
Over-designed systems for peak demand periods can result in wasted energy and resources during off-seasons.
How to Overcome It
- Scalable Storage: Modular stainless steel panel tanks can be added or removed based on production needs. This flexibility ensures that storage systems remain efficient year-round.
5. Meeting Sustainability Goals and Regulatory Requirements
Government regulations and growing consumer demand for sustainable practices add pressure to adopt energy-efficient and eco-friendly systems. However, achieving these goals can be challenging without disrupting operations.
Why This Is a Challenge
-
Transitioning to sustainable systems often requires significant upfront investment.
-
Maintaining compliance with multiple regulations across regions adds complexity.
-
Balancing sustainability with production efficiency can feel like a trade-off.
How to Overcome It
-
Energy-Efficient Designs: Beltecno’s insulated stainless steel tanks minimize heat loss and reduce the energy required to maintain consistent temperatures.
-
Recyclable Materials: Stainless steel is 100% recyclable, aligning with circular economy principles.
-
Incentives for Sustainability: Many governments offer tax breaks or subsidies for adopting eco-friendly systems. Beltecno’s solutions help manufacturers qualify for these incentives.
Meeting sustainability goals is not just about reducing environmental impact—it’s also a way to improve operational efficiency and strengthen brand loyalty.
Beltecno Global's stainless steel storage tanks and panel tanks, recognized among leading SS tank manufacturers, provide an innovative solution to the challenges of safe water storage and temperature management.
Their superior thermal properties, hygienic design, and energy-efficient features make them ideal for preserving beverage quality during the production process while reducing operational costs and environmental impact.
To learn more about how we can assist you in getting your perfect SS tank Contact Us today!