Water Tank Manufacturers: Transforming the Manufacturing Industry
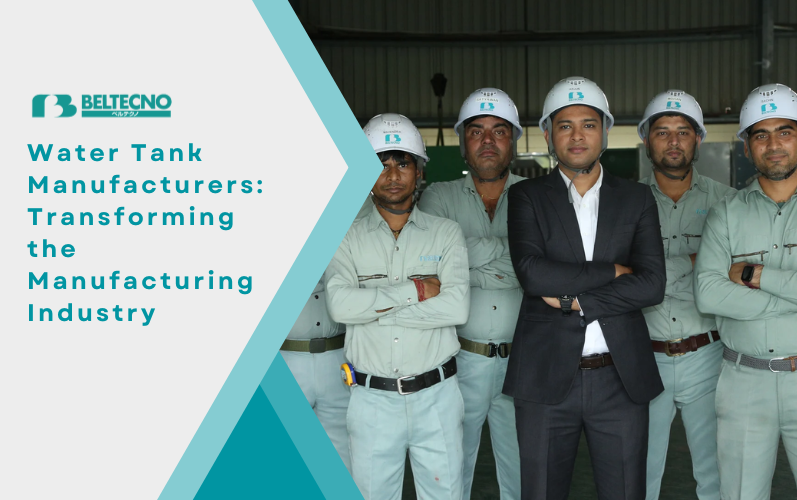
Industries today operate in a world where efficiency, sustainability, and innovation are key drivers of success. A critical but often overlooked component of industrial operations is water storage. Whether it’s for production processes, cooling systems, or sanitation, having reliable water storage solutions is non-negotiable.
Stainless steel water tanks have emerged as a game-changing solution in the manufacturing sector, thanks to their durability, hygiene, and adaptability. Behind these innovative solutions are water tank manufacturers who push the boundaries of technology and design to meet the diverse needs of industries.
In India, particularly in Delhi NCR, a hub for industrial and commercial activities, the demand for high-quality water tanks is growing rapidly.
This article explores the role of water tank manufacturers, focusing on their contributions, innovations, and how stainless steel tanks are shaping the future of industrial operations.
Stainless Steel Tank Trends in the Manufacturing Industry
The evolution of stainless steel tanks reflects broader industrial trends. From being mere storage units, these tanks have transformed into advanced infrastructure that supports industrial efficiency and sustainability.
1. Sustainability as a Core Priority
Environmental sustainability is a top concern for industries worldwide. Stainless steel tanks align with this goal as they are 100% recyclable, reducing waste and environmental impact. Moreover, their long lifespan minimises the need for frequent replacements, further conserving resources.
2. Advanced Manufacturing Techniques
Modern manufacturing techniques have significantly enhanced the quality and efficiency of stainless steel tanks. Processes like robotic welding, laser cutting, and modular design integration ensure precise construction and superior performance.
3. Focus on Customisation
Industries have unique storage needs, whether it’s for storing water or other industrial liquids. Water tank manufacturers like Beltecno India offer highly customisable tanks, enabling industries to optimise their storage solutions.
4. Integration of Smart Technology
The latest trend in tank manufacturing involves integrating IoT (Internet of Things) technologies. Smart water tanks equipped with sensors can monitor water levels, temperature, and quality, providing real-time data to industries for better resource management.
Delhi NCR, with its blend of traditional industries and modern technology hubs, serves as a microcosm of these trends, showcasing how stainless steel tanks are becoming a staple of industrial infrastructure.
The Process of Making Stainless Steel
Creating stainless steel is a step-by-step process that transforms raw materials into a durable, corrosion-resistant material used in everyday products like water tanks, appliances, and construction components. Here is an in-depth look at each stage of the process:
Step 1: Collecting Raw Materials
The first step involves gathering the necessary raw materials.
- Iron ore is the primary material and forms the base of stainless steel.
- Alloying elements such as chromium, nickel, and sometimes molybdenum are added to give stainless steel its unique properties. Chromium, for instance, makes the steel resistant to rust, while nickel adds toughness and molybdenum enhances chemical resistance in harsh environments.
This careful selection of materials ensures that the final product meets specific performance requirements.
Step 2: Smelting Iron Ore
Once collected, the iron ore is heated in a blast furnace at extremely high temperatures until it melts into molten iron. This smelting process separates the iron from impurities and prepares it for alloying. The molten iron forms the foundation for stainless steel production.
Step 3: Adding Alloying Elements
The molten iron is then mixed with alloying elements such as chromium and nickel. These additions are critical to achieving the properties that define stainless steel:
- Chromium: Provides corrosion resistance by forming a protective oxide layer on the steel surface.
- Nickel: Improves ductility and toughness, making the material more versatile.
- Molybdenum (optional): Enhances strength and chemical resistance for specialized applications.
By carefully controlling the proportions of these elements, manufacturers can tailor the stainless steel for various industrial uses.
Step 4: Purification
After alloying, the molten mixture undergoes purification to remove any remaining impurities. Advanced refining techniques ensure that the stainless steel is clean, strong, and free of defects. This step is vital for producing high-quality stainless steel that meets strict industrial standards.
Step 5: Cooling and Shaping
The purified molten steel is then cooled and shaped into different forms depending on its application. These include:
- Sheets: Used in appliances, construction, and fabrication.
- Bars: Essential for industrial tools and structural components.
- Coils: Often used in manufacturing processes requiring flexibility.
This step transforms the raw material into versatile building blocks for numerous industries.
Step 6: Heat Treatment
To further enhance its properties, the formed stainless steel undergoes heat treatment. This process involves controlled heating and cooling to:
- Increase the material's strength.
- Enhance resistance to rust, wear, and tear.
- Improve the steel’s ability to withstand extreme conditions.
The heat treatment gives the steel its final mechanical and physical characteristics, making it ideal for demanding applications.
Step 7: Cutting and Shaping
In the final step, the stainless steel is cut and shaped into finished products. Using advanced machinery, manufacturers create water tanks for industrial and commercial storage. This step ensures the stainless steel meets specific design requirements and is ready for end use.
Benefits of Stainless Steel Tanks for the Manufacturing Sector
Stainless steel tanks are not just a storage solution, they are a strategic investment for industries looking to enhance efficiency, hygiene, and sustainability. Here’s a closer look at the benefits they offer:
1. Exceptional Durability
Unlike plastic or concrete tanks, stainless steel tanks can withstand harsh environmental conditions, including extreme temperatures, UV exposure, and chemical reactions. Their corrosion resistance ensures a long lifespan, making them ideal for industries that require reliable storage solutions over decades.
2. Hygienic Water Storage
Hygiene is critical in industries like pharmaceuticals, food processing, and healthcare. Stainless steel’s non-porous surface prevents the growth of bacteria, algae, and other contaminants, ensuring water quality remains uncompromised.
3. Customisation and Scalability
Manufacturers can design stainless steel tanks in various shapes, sizes, and configurations to meet specific industrial needs. Whether it’s a modular panel tank for large-scale applications or a cylindrical tank for smaller operations, customisation options are virtually limitless.
4. Cost-Effectiveness Over Time
While stainless steel tanks may have a higher upfront cost compared to alternatives, their low maintenance requirements and longevity make them a cost-effective solution in the long run.
5. Versatility Across Applications
From storing potable water to handling industrial chemicals, stainless steel tanks can be adapted for various uses. Their versatility makes them an indispensable asset for industries across sectors.
Role of Water Tank Manufacturers in India
India’s industrial landscape has grown exponentially over the past few decades, and water tank manufacturers have played a crucial role in supporting this growth.
-
Catering to the Unique Needs of Indian Industries
Water tank manufacturers in India understand the diverse challenges faced by industries, from water scarcity to fluctuating environmental conditions. By offering durable and efficient solutions, they ensure uninterrupted operations across sectors.
-
Focus on the Delhi NCR Region
Delhi NCR stands out as a key market for water tank manufacturers. The region's rapid industrialization and urbanisation have created a significant demand for high-quality water storage solutions. From large manufacturing plants to residential complexes, stainless steel tanks are being adopted at an unprecedented rate.
-
Export Potential
Indian water tank manufacturers are not just catering to domestic markets but are also making their mark globally. The combination of cost-efficiency and high-quality production has made India a preferred destination for water tank imports.
Choosing the Right Water Tank Manufacturer
Selecting a water tank manufacturer is a critical decision that can impact the efficiency and longevity of your storage solution. Here’s what to consider:
1. Quality Certifications
Ensure the manufacturer complies with national and international quality standards. Certifications are a testament to their commitment to excellence.
2. Customisation Options
A good manufacturer should offer a range of designs and configurations to suit your specific needs.
3. After-Sales Support
Look for manufacturers who provide comprehensive warranties and reliable customer service.
4. Reputation and Experience
Research the manufacturer’s track record. Established brands like Beltecno are known for their reliability and expertise.
Beltecno: Pioneers in Water Tank Manufacturing
Among the leading names in water tank manufacturing, Beltecno has established itself as a trusted brand. Known for its focus on quality, innovation, and customer satisfaction, Beltecno has become synonymous with excellence in stainless steel tanks.
-
State-of-the-Art Facility in Neemrana
Beltecno’s manufacturing unit in Neemrana is a testament to its commitment to quality. The facility is equipped with advanced machinery and adheres to stringent quality control processes, ensuring every tank meets international standards.
-
Specialisation in Stainless Steel Panel Tanks
Panel tanks are one of Beltecno’s flagship products. These modular tanks are easy to transport, assemble, and maintain, making them ideal for industries requiring large-scale water storage.
-
Focus on Innovation
Beltecno continually invests in R&D to stay ahead of industry trends. From using precision welding techniques to developing insulated tanks, the company sets benchmarks for others to follow.
Future of Water Tank Manufacturing in India
The future of water tank manufacturing is bright, driven by advancements in technology and growing awareness about sustainability.
Technological Innovations
Automation, robotics, and IoT integration are expected to revolutionize tank manufacturing processes, enabling more precise and efficient production.
Sustainability as a Driving Force
Manufacturers are exploring eco-friendly materials and energy-efficient production methods to align with global sustainability goals.
Expanding Market Demand
With industrial and urban development continuing at a rapid pace, the demand for high-quality water storage solutions will only grow, particularly in regions like Delhi NCR.
Conclusion
Stainless steel water tanks are more than just a storage solution—they are a vital component of industrial infrastructure. With their durability, hygiene, and versatility, these tanks have become a preferred choice across sectors.
Water tank manufacturers, especially in Delhi NCR, are driving this transformation by delivering innovative and reliable solutions. Among them, Beltecno stands out for its commitment to quality and excellence.
Whether you’re looking for a durable water tank for industrial use or a customised solution for commercial projects, choosing the right manufacturer is crucial. Partner with trusted names like Beltecno to meet your water storage needs efficiently and sustainably.
To learn more about how we can assist you in getting your perfect SS tank please Contact Us.