Research & Development
R&D Function
We Offer
Durability
Lightest Panel Tank
Customisation
Development Process
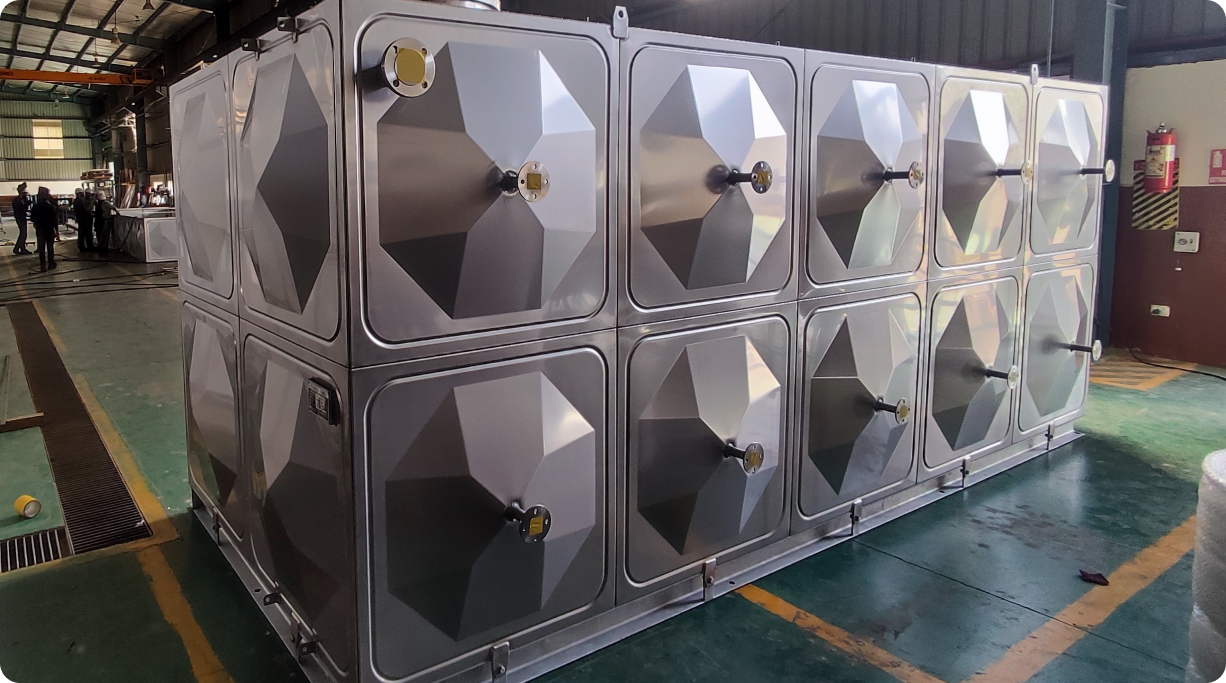
Process 1
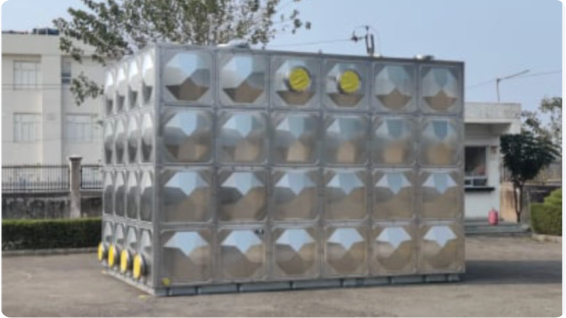
Chemical anchor bolt installation
Drive the required number of anchor bolts into a solid foundation at the specified positions and depths.
Wait the specified time for the chemical to harden without touching the anchor bolt.
Process 2
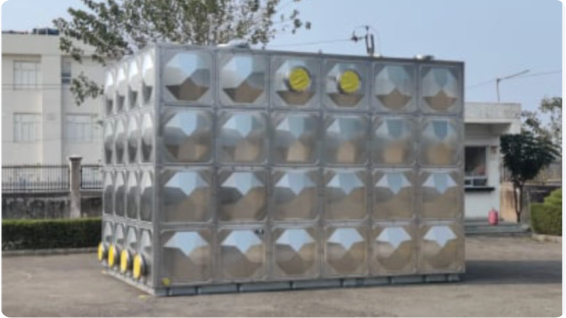
Assembly of the support base
Check the foundation level with a spirit level and place the components in their installation positions.
Adjust the liner to align the receiving platform level.
Temporarily tighten the parts and check the diagonal with a tape measure, then secure each bolt.
Then check the level again with a spirit level.
Process 3
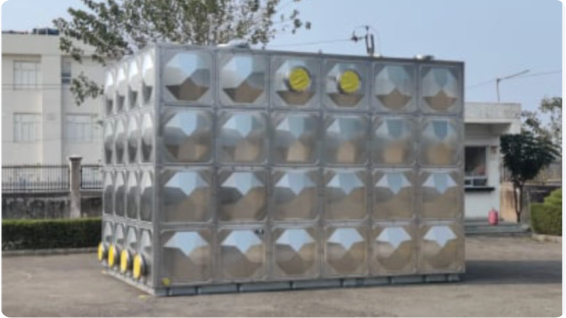
Bottom plate assembly
Place the bottom plate according to the shop drawing. The bottom plate is tack-welded and then permanently welded.
Process 4
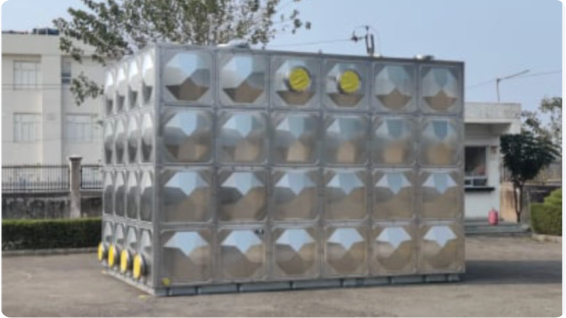
Side plate assembly
The second and third rows are temporarily welded from the bottom up and then assembled.
Then, the actual welding is performed.
The panel is supported from the outside and welding is done from the inside of the panel.
Process 5
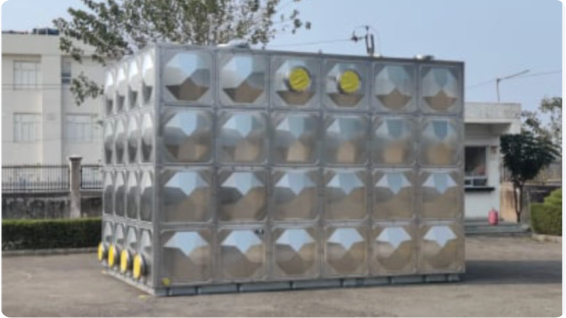
Ceiling welding
Tack weld the ceiling panel to the upper side panel.
Set up temporary pillars if necessary.
Check the diagonal dimensions of the upper side panel and then perform the actual welding.
The welding is done from the inside of the panel.
Process 6
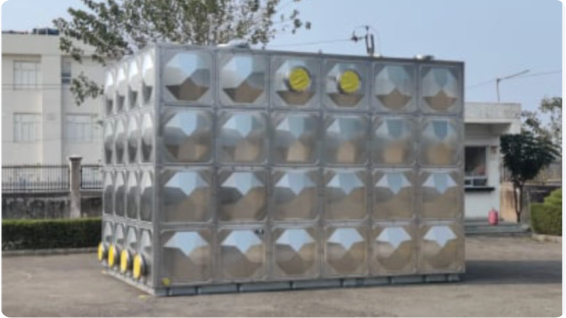
Internal reinforcement welding
Check the production drawings and weld the columns and beams in the designated locations
Process 7
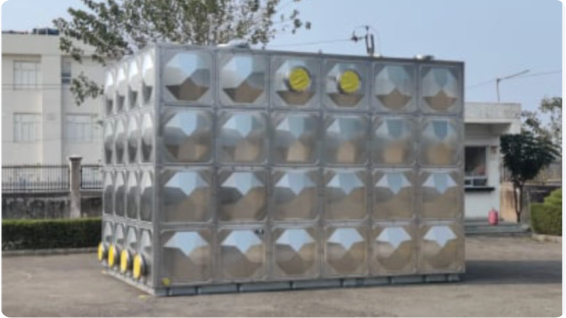
Water filling inspection and welding treatment (acid pickling)
After filling the tank with water and allowing a certain amount of time to pass, visually check for any leaks.
Once you have confirmed that there are no leaks, drain the water.
Remove burns from welds.
The pickling solution is applied, waited for a specified time, and then washed off.
Process 8
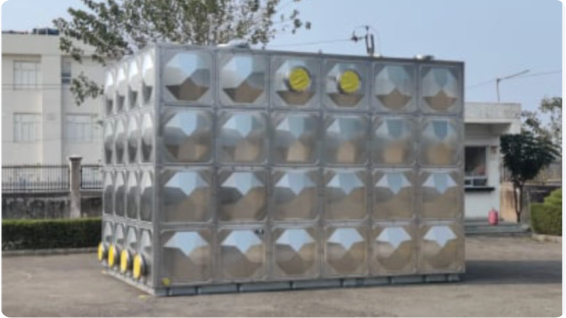
Tank completed
Based on the production drawings, confirm the dimensions and mounting positions of each outlet and internal reinforcement.
Check the dimensions and number of accessories.
Install the nameplate.
Check the appearance of the tank.
Fully Welded Assembly
All parts are joined together by special welding
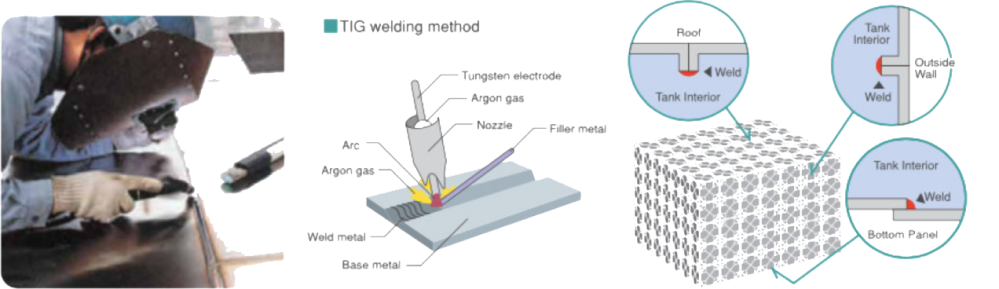
The tank body is constructed through the process of TIG welding which joins together corrosion resistant, highstrength stainless steel panels that are press formed into a unique diamond cut shape
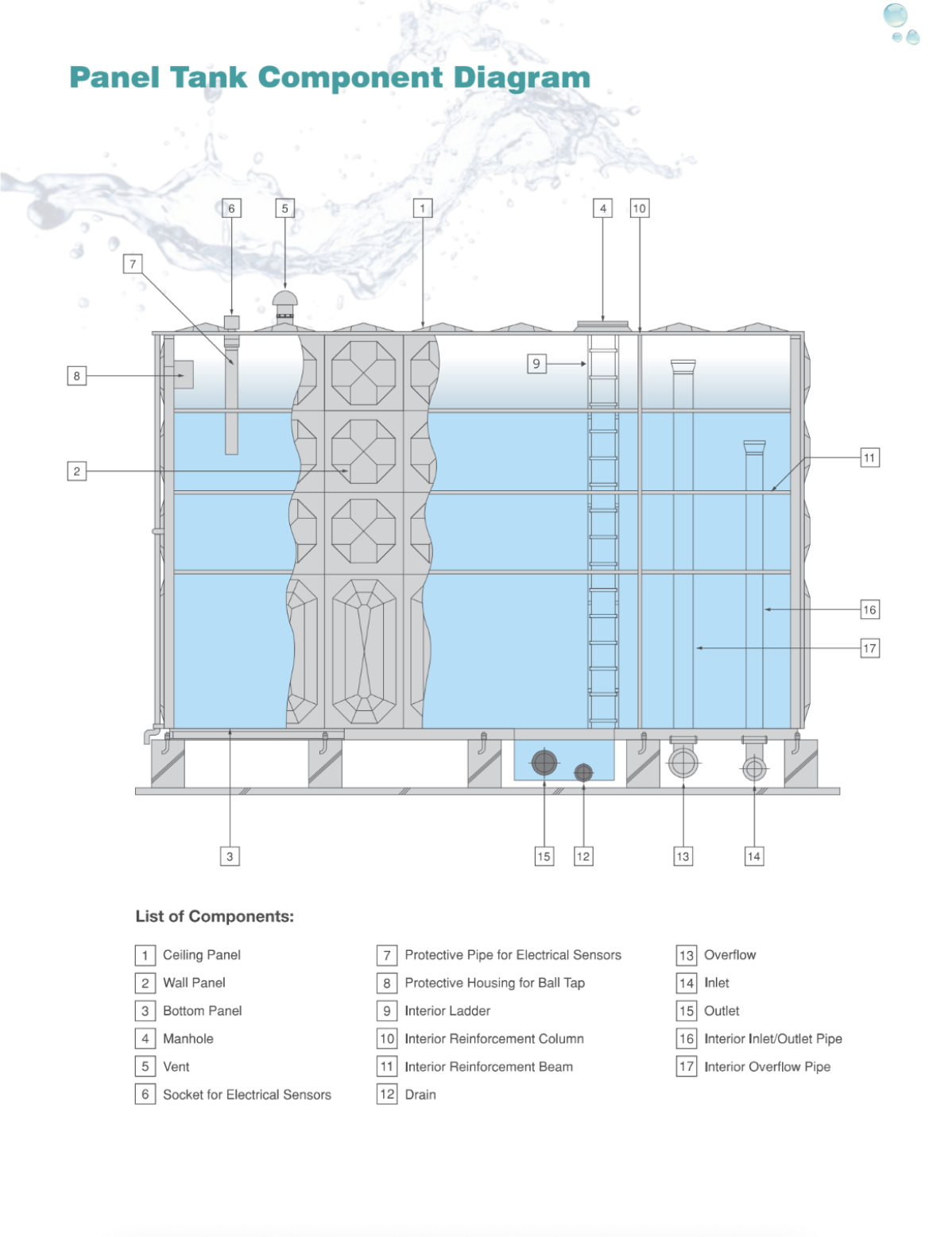
Dispatch Process
Explore All Sizes of Tanks
Frequently Asked Questions
What is the durability of the panel tanks?
How does this tank be better than plastic and concrete?
Panel tanks are hygienic as they are made of food-grade stainless steel grades SS304 and SS316L which helps to preserve water in its natural form, unlike plastic tanks.
Lightweight: 1/30 the weight of concrete.
Fast Installation: 1/3 the time of Concrete Construction.
Economic: Life Cycle Cost is less than a Concrete Tank.
Will there be any leakage in the tank in the future?
How do I clean the tank?
The maintenance of stainless steel tanks is much cheaper, we provide inside and outside ladders to get into the tank and clean it.
What is the process for Buying Stainless Steel Panel Tank?
For quotaion, there are certain basic specifications are required from customer's side.
1) Total Volume required
2) Which Stainless Steel Grade is required (SS 304 L or SS 316 L)
3) What Type of water to be stored in the tank.
*We recommend RO/Treated/ Corporation Water/ Process Water to store in Stainless Steel Tanks.
How the panels are joint togeater ?
Stainless Steel Panel Tanks are made of Stainless Steel Panels (1 mtr. x 1 mtr.) using Tig welding by our certified expert welders.
Get notified of new blog updates.
Be the first to know what's going on in the water industry. We regularly post useful updates on the industry as well as product information. Enter your email ID and hit the subscribe button to be a part of this change from traditional water storage to a stainless steel water storage solution.